The 6 Most Common Compressed Air Drying Methods
Water is a challenge in every air compressor system. As air is compressed, water is created in the air stream. During cooling, that water condenses and mixes with the compressed air delivered to your tool or application. Some water is okay for most applications, but too much water can be a problem. That’s where compressed air drying comes in!
There are six common ways of removing or reducing the amount of water in a compressed air stream. The common compressed air drying methods are:
- Aftercooler
- Air-Cooled
- Water Cooled
- Storage Tank Cooling
- Membrane Type Dryer
- Refrigerant
- Deliquescent / Absorption Drying
- Regenerative / Adsorption Drying
- Dual Tower Regenerative Desiccant Air Dryers
Each of these drying methods is unique, with its own benefits and disadvantages. This article will explain each standard air drying method in more detail.
Aftercooler Method
In the aftercooler method, a heat transfer will occur between two bodies of different temperature air until temperature equilibrium is reached. This transfer of heat can take place in three different ways and, generally, these take place simultaneously:
- Conduction
- Convection
- Radiation
Aftercoolers use this principle to balance the temperature of compressed air with atmospheric air, and some moisture separation also occurs within the process.
An aftercooler is a heat exchanger used to cool compressed air and minimize moisture within the system. Reduced compressed air temperatures cause water droplets to precipitate out of the air. These liquid contaminants are typically collected and drained off with a moisture separation device and drain trap (mechanical or timed).
Figure 1. Typical mechanical float-type drain trap
Figure 2. Typical electrically timed drain trap
Aftercoolers are a popular choice for mobile air compressors and can also be used in stationary applications. The aftercooler should be located as close as possible to the compressor outlet.
Air-Cooled Aftercoolers
The air-cooled aftercooler looks like a car radiator and also acts like one. However, rather than coolant filling the interior tubes, the hot compressed air enters the bottom of the air-cooled aftercooler and tube system, discharging through the upper discharge port into a moisture separator.
As heat from the compressed air transfers to the cooler atmospheric air, some of the heat of compression and resulting moisture is removed from the compressed air and carried away.
Some air-cooled aftercoolers use electrically powered 12V or 24V fans to push air through the system. The tubes have fins or metal plates in between them to increase their surface area and dissipate the heat more effectively.
Air-cooled aftercoolers are commonly used with mobile air compressor systems because they are effective, easy to source, cost-effective, and relatively straightforward to install.
Water-Cooled Aftercoolers
Water-cooled aftercoolers do the same thing as air-cooled aftercoolers, only with more control of the discharge air temperatures. The primary difference is that water-cooled aftercoolers use a liquid coolant that flows through a shell and tube or a plate-fin design heat exchanger to absorb the heat of compression from the compressed air volume.
Advantages & Disadvantages of Aftercoolers
Advantages
- Reduces heat and moisture within the system
- Easy to source
- Cost-effective
- Straightforward addition to most compressed air systems
- Fan-less systems don’t require electricity
- Efficient heat transfer
Disadvantages
- Difficult heat recovery
- Requires clean, fresh atmospheric air
- Requires a high volume of water (water-cooled only)
Storage Tank Cooling Method
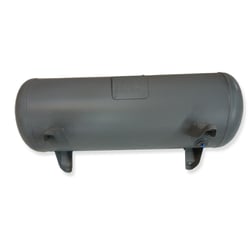
Figure 4: VMAC’s 10-gallon air receiver tank with mounting feet
The storage tank cooling method of drying compressed air uses an air receiver tank to turn some of the moisture that may be present in the air into water droplets as the air comes from the compressor or carries over from the aftercooler.
When air leaving the aftercooler enters the receiver tank, it comes into contact with the colder steel wall of the tank, which is usually at ambient temperature. At this point, moisture starts to condense out of the compressed air as the air chills.
If the air stays in the tank for enough time, the air temperature in the tank will match the ambient temperature, and no more moisture will condense out. At this point, the air in the receiver tank is 100% saturated at a dewpoint equal to atmospheric temperature, which results in water formation.
The water must be drained out of the air receiver tank after use. The storage of condensation and moisture in air receiver tanks leads to the formation of rust and scale on the inside of the tank, which can become loose and get carried downstream in the outgoing air. The water can also freeze in colder temperatures. This rust, scale, and ice can cause blockage problems in air-using components and premature wear on filters.
Mobile air compressor systems with an air receiver tank automatically employ the storage tank cooling method, which is an inexpensive and simple solution. However, the efficiency of this method will depend on the amount of time air is stored in the tank before use, and some applications will still require an aftercooler.
Advantages & Disadvantages of Storage Tank Cooling Method
Advantages
- Air receiver tanks are inexpensive
- Air receiver tanks are easy to source
- Simple and straightforward
- Often pre-built into mobile air packages
Disadvantages
- Air receiver tanks can take up considerable amounts of space
- Not the most effective or efficient way to separate water
- Requires tank to be drained manually every day it is used
Membrane Type Air Dryers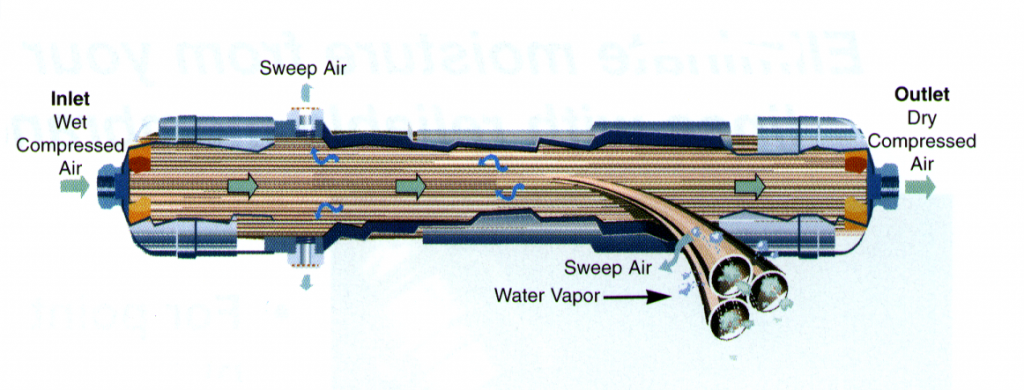
Figure 5: Cross-section diagram of a membrane dryer
The membrane dryer operates on the principle of selective permeation through a membrane.
As the compressed air passes through a bundle of tiny hollow (polysulfone) membrane fibers, water vapor and a portion of the compressed air flow diffuses through the semi-permeable membrane walls while the dried air continues downstream.
The water vapor separated from the compressed air by the differential gas pressure on the inside and outside of the hollow fibers is purged out of the housing by the sweep air (purge air).
The membrane dryer can only be used with clean, oil-free air. It must have a coalescing prefilter installed ahead of the dryer to remove any liquid water, oil, and aerosol contaminants from the compressed air stream, as these would block the permeation of the fibers, reducing the performance of the dryer.
These dryers are point-of-use dryers, sized for low capacities compared to other dryer types. Membrane dryers can be connected in parallel to increase the capacity beyond a single dryer.
Membrane dryers are used quite effectively in larger railway and bus applications and in larger vehicles, such as mobile service trucks, mining vehicles, firefighting trucks, and agricultural vehicles. Membrane dryers are also suitable for many stationary applications.
Advantages & Disadvantages of Membrane-Type Dryers
Advantages
- No moving parts
- No consumables to replace
- No external power source required
- Can operate in severe environments, such as high or low temperatures or corrosive and explosive atmospheres
- Dewpoint suppression range is between +40°F and -40°F
Disadvantages
- Requires oil-free air
- Some models require (consume) about 15-20% of the purge air
- Membrane dryers reduce the oxygen content of the compressed air and cannot be used in breathing air applications
Note: Air aftercoolers, storage tank cooling, and membrane drying are the three most common methods for cooling compressed air in mobile applications. The remaining compressed air cooling methods mentioned in this article are typically used in stationary setups.
Refrigeration Drying
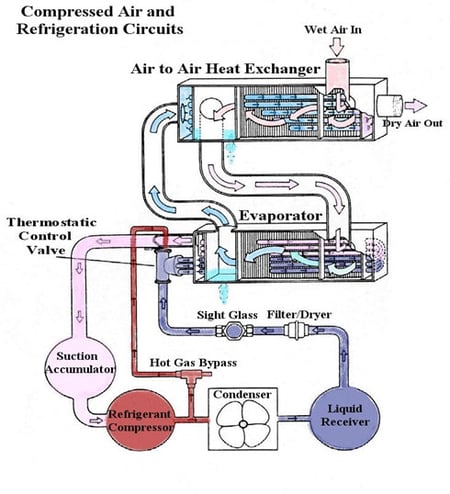
Figure 6: The Typical Flow Pattern – The Refrigeration Cycle
Refrigeration drying occurs as part of the refrigeration cooling process, with the two systems working symbiotically.
There are two types of refrigerated air dryers: Cycling and Noncycling. Both types use a refrigeration system to cool the compressed air to a temperature as close to freezing as possible to condense out as much water as possible.
Most refrigerated dryers provide a pressure dew point of 35°F, but some less expensive models with smaller refrigeration systems are rated for the higher dewpoint of 50°F.
In a refrigeration system, hot compressed air enters the air-to-air heat exchanger and flows down the inner tube of a tube-in-tube bundle. The incoming hot air is re-chilled by the air traveling in the outer tube, which the refrigeration section has cooled.
As the air cools, water vapor condenses into liquid droplets. The condensed liquid droplets are then removed from the air stream in a separator and automatically discharged to drain by an automatic condensate drain trap. This pre-chilling allows for the use of a smaller refrigeration unit and increases the dryer package’s efficiency.
The pre-cooled compressed air then enters the air-to-refrigerant heat exchanger, where the heat is removed directly from the compressed air by the refrigeration system down to +35°F.
As the air continues to cool, water vapor again condenses into liquid droplets. The condensed liquid droplets are then removed from the air stream in another separator and automatically discharged to drain by an automatic condensate drain trap.
Finally, the air passes through the secondary side of the air-to-air heat exchanger, where it is re-heated by the incoming hot air. The re-heating of the outgoing air prevents downstream pipe sweating and increases the air’s effective volume, enabling it to do more work. It will take longer for a pipe exposed to cool atmospheric temperatures to drop from the re-heated temperature to a point less than +35°F.
Advantages:
- Constant dewpoint of +35°F to +50°F (dependent on ISO class)
- Low maintenance costs, with no chemical or desiccants to add or replace
- No recurring costs other than electricity
- No after filter required (a coalescing type prefilter is recommended)
Disadvantages:
- Lowest dewpoint available is +35°F but any lower and the air-to-air heat
exchanger will freeze up - Some dryers have shown a problem with refrigerant leakage
Deliquescent / Absorption Drying
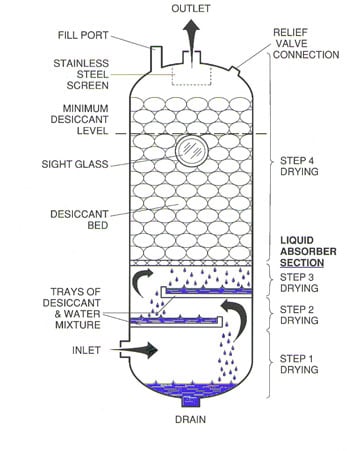
Figure 7: A Typical Deliquescent Type Air Dryer – Absorption Type
Another common way to dry air is through absorption. With absorption drying, incoming air enters the vessel near the base and passes through a mechanical separation section. The free liquids and solids drop to the bottom of the vessel due to expansion. To some degree, this constitutes a pre-drying of the air.
The air enters the desiccant bed of deliquescent materials, such as water-soluble salts or shotted urea. These hygroscopic chemicals condense water vapor as they deliquesce or dissolve the liquid.
Absorption occurs until the deliquescent materials are consumed and require replacement.
Advantages:
- Low initial cost
- No electrical hook-up
- No moving parts
- Simple operation
Disadvantages:
- Dewpoint suppression is between 20°F-30°F (on average)
- Deliquescent material must be added to or replaced as it absorbs and melts
- Downtime required to replace deliquescent material
- Ecological problem of disposing of the dissolved deliquescent material
- Cost of replacement deliquescent and disposal of dissolved deliquescent
material - Carryover of corrosive deliquescent materials into the downstream piping network
and air using components - Parts of the deliquescent materials can solidify in the bed, causing channels for
the air to by-pass most of the drying material, which reduces the dryer’s performance
Regenerative / Adsorption Drying
Desiccant Air Dryers
Desiccant dryers lower the dewpoint of compressed air by adsorbing water vapor onto the surface of a desiccant. The three basic types of desiccant used in dual tower regenerative air dryers are:
- Activated Alumina
- Silica Gel
- Molecular Sieve
The process of adsorption begins as the water vapor, highly concentrated in the compressed air stream, moves into an area of lower water vapor concentration in the pores of the desiccant.
Once inside the pores, a natural attraction of the vapor molecules to the solid surface of the desiccant causes water vapor molecules to build upon the surface of the desiccant. As enough molecules gather, vapor changes phase and becomes a liquid. The process continues as long as the water vapor concentration in the air is greater than the concentration in the desiccant pores.
The water remains on the surface of the desiccant until it is stripped off. This stripping is called reactivating or regenerating the desiccant. Reactivating the desiccant means it may be used again and again.
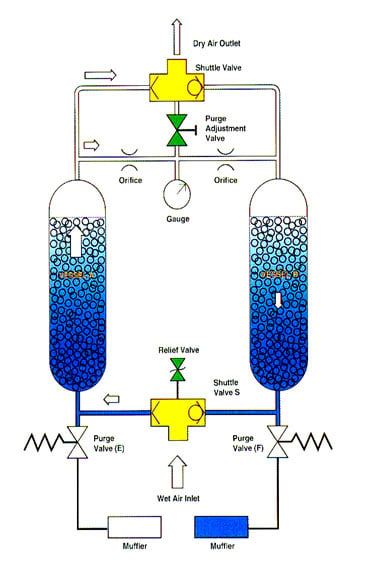
Figure 8: Dual Tower Desiccant Air Dryer Diagram
Dual Tower Desiccant Air Dryers
Dual tower desiccant air dryers have many names, including pressure swing, regenerative, and instrument air dryers. Both heated and heatless models are available. Despite the varied terminology, all desiccant dryers offer a continuous supply of dry compressed air by using two identical towers containing a bed of desiccant beads.
While one tower is on stream drying the compressed air, the other tower is off stream so the desiccant in that tower can be regenerated. The regeneration of the desiccant bed is accomplished by expanding some of the dried air to near atmospheric pressure and directing it across the wet desiccant bed. This swing in pressure produces expanded air, called purge air, with a very low water vapor concentration.
Imagine that the air used for the purge flow is 80°F and has a dewpoint of -40°F at 100 psig. This purge air is then expanded from 100 psig to a couple of pounds pressure, heated to a temperature of between 350-600°F, and passed counter-currently through the wet desiccant bed. The moisture-holding capability of this superheated, dry, expanded air is extremely high.
The hot air’s vapor pressure is so low in comparison to that of the desiccant that the moisture moves from the area of higher vapor pressure (the desiccant) to that of the lower vapor pressure (the hot purge air). The purge air stream then carries the water vapor out of the dryer.
Dual tower desiccant air dryers typically dry instrument air and process air, and is used in applications where airlines are exposed to low ambient temperatures, below 32°F, and in other critical applications. Typical dewpoints produced by these types of dryers are -40°F to -100°F, although lower dewpoints are possible.
Advantages & Disadvantages of Desiccant Air Dryers
Advantages
- Can operate a very low dewpoint in below-freezing temperatures
- Delivers extremely dry air that meets ISO Quality Classes 1, 2, & 3
Disadvantages
- High purchasing costs
- High operation costs
- Ongoing maintenance costs
Additional Resources
You may also be interested in the following resources:
- Why Is There Water In My Compressed Air?
- Compressed Air Aftercoolers
- FRL: Filter Regulator Lubricators
- And more…!