Compressed Air Aftercoolers
What are compressed air aftercoolers, and why are they required? This article will tell you everything you need to know about aftercoolers; discover the two most common types, find out why air aftercoolers are important, and learn their role within an air compressor system.
What Is An Aftercooler?
An aftercooler is a mechanical heat exchanger designed to remove the heat and moisture of compression from a compressed air stream so the air is cool and dry enough for use in air-operated equipment.
A compressed air aftercooler has three primary functions:
- Cool the air discharged from the air compressor
- Reduce the moisture in compressed air
- Protect downstream equipment from excessive heat and moisture
Why Are Air Aftercoolers Required?
Compressed air discharged from an air compressor is always going to be hot. However, the exact temperature will vary according to the type of compressor used.
Typical Compressor Average Outlet Temperatures:
Oil-Injected Rotary Screw 200°F
Oil-Free Rotary Screw 350°F
2-Stage Reciprocating 300°F
Centrifugal 225°F
High-temperature air is typically not usable in air-operated equipment, as heat detrimentally impacts equipment lubrication and sealing materials. Hot air also contains large quantities of moisture vapor which, as it condenses, contributes to rust, scale build-up, washing out of lubricant, and possible freezing issues.
Water exists in a vapor state in all atmospheric air. As the air is drawn into a compressor and pressurized, this moisture becomes more concentrated. Due to the high temperature of the air after compression, the moisture remains in a vapor state, above the dew point temperature.
The dewpoint is the temperature at which air becomes saturated at 100% of its capacity to hold water in a vapor state. A general rule is that for every 20°F rise in temperature, the air can hold twice the moisture load in a vapor state above the dewpoint.
However, as the compressed air cools, the dewpoint lowers, and water vapor condenses. When the amount of moisture in the air exceeds the dewpoint, the water vapor turns into water droplets, which must leave the compressed air.
For example, a 200 CFM air compressor operating at 100 PSIG can result in as much as 45 gallons of water in the compressed air system each day without an aftercooler.
Types Of Aftercoolers
The two most common types of aftercoolers are air-cooled and water-cooled.
Air-Cooled Aftercoolers
Air-cooled aftercoolers use ambient air to cool the hot compressed air. Compressed air enters the air-cooled aftercooler and travels through either a spiral finned tube coil or a plate-fin coil design, while ambient air is forced over the cooler by a motor-driven fan. The cooler ambient air removes heat from the compressed air.
Most air-cooled aftercoolers are sized to cool the compressed air to within 15°F to 20°F of ambient cooling air temperature, also called approach temperature. As the compressed air cools, up to 75% of the water vapor condenses into a liquid that should be removed.
A moisture separator installed at the discharge of the aftercooler mechanically removes most of the liquid moisture and solids from the compressed air.
The moisture separator utilizes centrifugal force, and in some cases baffle plates, to collect moisture and solids at the bottom of the separator. An automatic drain should then be used to remove the moisture and solids.
Belt Guard Air-Cooled Aftercooler
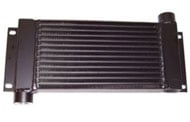
Source: AKG / akgts.com
A belt guard air-cooled aftercooler mounts to the compressor’s v-belt guard. The compressor’s belt pulley has fins designed to force ambient air over the compressor and air-cooled aftercooler. The air passing over the aftercooler facilitates the heat transfer. The pulley also sends air over the compressor helping maintain proper operating temperature.
Water-Cooled Aftercooler
Water-cooled aftercoolers are similar to air-cooled aftercoolers but are often used in stationary compressor installations, where cooling water is available. There are a few advantages to using water as the cooling media:
- Water has minimal seasonal fluctuation in temperature
- Cold water is cost-effective and available in large volumes
- Cold water can efficiently approach the ambient air temperature, which eliminates condensation downstream
Water-cooled aftercoolers typically have an approach temperature between 10°F and 15°F, which is also beneficial when cooler air is required.
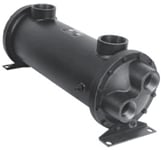
Source: Southwest Thermal Technology quincyaftercoolers.com
Water-cooled aftercoolers come in several different styles. The most common style is a Shell and Tube aftercooler. This aftercooler consists of a shell with a bundle of tubes fitted inside. The compressed air flows through the tubes in one direction as water flows through the shell in the opposite direction.
During this process, heat from the compressed air is transferred to the water. As the compressed air cools, liquid water forms within the tubes. The moisture is then removed by a moisture separator and drain valve, just like with air-cooled aftercoolers.
How To Size An Aftercooler
Aftercoolers require three metrics for proper sizing: CFM, PSI, and temperature. The CFM and PSI are straightforward, as they are determined by the air compressor’s output for the application. Meanwhile, the temperature metric requires additional considerations.
Coolers are usually sized with Cold Temperature Difference (CTD) of 10°F, 15°F or 20°F. This means that the compressed air temperature at the aftercooler outlet will be equal to the cooling medium temperature plus the CTD when sized for the specified inlet air temperature and flow. The lower that temperature needs to be, the larger the aftercooler needs to be.
The required compressed air temperature is often determined by other components downstream in the system. Each component’s maximum temperature must be determined and considered to discover the true temperature requirements for the aftercooler—this step is critical.
Disclaimer: Individual air compressor components may vary from the chart above; always check with the component manufacturer for specs and tolerances, including typical and maximum operating temperatures.
Once the aftercooler requirements are understood, choose an aftercooler with specs that meet or exceed these requirements. Compressor manufacturers may already consider common aftercooler requirements and include aftercoolers as a component of the compressor system. Otherwise, a stand-alone or freestanding aftercooler will need to be purchased and installed downstream of the compressor.
VMAC’s Air Aftercoolers
VMAC offers 70 CFM and 185 CFM air aftercooler options for mobile air compressors. Both aftercooler models were designed to improve air performance and extend the life of air tools by removing up to 80% of the moisture from compressed air. Follow the links below to learn more:
Want to learn more about air compressors? Check out our other air compressor articles!