Why Is There Water In My Compressed Air?
People have tolerated water in their compressed air lines for so long that many consider the problem a necessary nuisance. Some operators have just accepted that their tools drip or spew hot water or that they need to drain the water out of their air compressor receiver tank regularly. While this may be normal for some air compressor brands, it is unnecessary.
Why Is There Water In My Air Lines?
The air around you is made up of more than just oxygen—atmospheric air also includes water vapor, oils and other vapors, and dust and dirt. The water in our air plays an important role in our climate systems, impacting temperatures, humidity, rain and weather patterns, radiation, and more.
When air is compressed, water gets separated from the compressed air, and this water can end up in air lines, receiver tanks, and pneumatic tools if it isn’t properly filtered out.
Having a small amount of water in the compressed air is okay for many applications. However, if you see dripping or your application requires clean, dry air, you may need to upgrade your air compressor system with filters, aftercoolers, or air dryers.
How Is Water Created During Air Compression?
Let’s talk about how compressing air creates water. We’ll start with an example using one standard cubic foot of atmospheric pressure air—Figure 1 below—and see what happens when we make it into usable, compressed air.
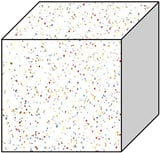
Figure 1
Before compression, our cubic foot of air exists completely invisible to the naked eye and is comprised of:
- Air / Oxygen
- Water vapor
- Oils and other vapors
- Dust and dirt
After compression, the volume of the air has changed, but the amount of water, vapors, dust and dirt has not changed in volume. Instead, these contaminants have become more concentrated, as we end up with the same amount of water and contaminants in a much smaller amount of air—see Figure 2.
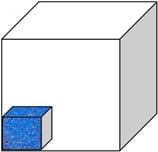
Figure 2
In fact, the compressed air can hold even more water now because of two physics truths:
- Hot air holds more water vapor than cool air
- The act of compression generates heat
Air gets hot when it’s compressed, allowing it to hold more water vapor. In our example, we still have a tenth of the amount of air, but the same amount of water, making the air more humid. But how does this water vapor condense to become liquid water?
Compressed air is hotter than the air surrounding the compressor, which means it will rapidly cool when it leaves the compressor. (Many air compressor systems are also designed to help this air cool even faster.) As the compressed air cools down, it can no longer hold the same amount of water vapor, so the extra moisture gets forced out of the air in liquid form.
You likely already know this process as “condensation,” and it’s the same natural process that causes dew on early morning grass or water droplets on an ice-cold beer glass. By the time compressed air has cooled to the temperature range typical for pneumatic tools, which is about 120°F and below, quite a bit of water has formed through condensation.
What Happens To Contaminants During Compression?
Let’s look again at our example of compressed atmospheric air. We know the atmospheric air became compressed air when it was forced into a smaller volume, and that water vapor transformed into water droplets when the heated air was cooled. But what happened to the other contaminates, like oil, dust and dirt, that didn’t compress?
It’s simple: they were filtered out or exited the air compressor. Most contaminants get trapped in an intake filter, preventing dirt, dust, and other airborne contaminants from entering the system in the first place.
Contaminants that do bypass the intake filter and enter the air compressor system typically get filtered out through an additional filtration system, such as an oil filter, or they leave the system as part of the compressed air.
Each air compressor system is set up differently, so if you're curious about a specific air compressor's filtration system, talk to the manufacturer. You can also learn more about compressed air treatment methods here.
How Is Water Removed From Air Compressor Systems?
Water is a natural occurrence in compressed air. It’s not something you can prevent, but you can take measures to remove water droplets and other concentrated contaminants before they reach your air tools or other applications.
It's critical to pay attention to water in your compressed air. Water can cause rust and damage to air compressor systems and tools, and hot discharged water can be dangerous to operators. In addition, this water can cause tools to freeze up in the winter.
When your application requires less water in the compressed air, several options exist for removing the water from air compressor system.
One option is an aftercooler, which cools air from 200-350°F to a usable temperature around 15-20°F above the ambient temperature, and removes most of the moisture that is created during this cooling. For most applications, an air aftercooler will eliminate enough water to operate pneumatic tools safely.
A Filter Regulator Lubricator, or FRL, can also help remove water. Although an FRL isn’t as effective in water removal as an aftercooler, it has several additional benefits: FRLs filter solid contaminants, remove oil vapors, regulate pressure, and lubricate the compressed air with tool oil if required.
Some air compressor systems that require an air receiver tank, like a reciprocating air compressor, will also rely on the receiver tank to collect and trap water before it reaches your air tools. This trapped water is then released through a drainage valve that you must manually open and close.
Air compressor applications that need exceptionally dry air may also use a refrigerated air dryer, an absorption air dryer, or both. You can learn more about these common air drying methods here.
Do I Need To Drain The Water In My Air Compressors?
Whether you need to drain the water created by compressed air depends on your air compressor. If you have an air compressor with an air receiver tank that collects water, you will need to follow the manufacturer’s guidelines to determine how often the air receiver tank should be drained. Many air tank manufacturers recommend draining the tank daily and before long-term storage.
Government regulations may also determine when water in the air receiver tank must be drained. For example, OSHA states in 1910.169(b)(20), “The drain valve on the air receiver shall be opened and the receiver completely drained frequently and at such intervals as to prevent the accumulation of excessive amounts of liquid in the receiver.”